COEX-ACCUMULATOR HEAD
The COEX-Accumulator Head is designed for 2 up to 5 layer discontinuous coextrusion. The COEX-Heads work to the „first in/first out“ system. The melt guides are free of any obstructions completely preventing flow marks. The melt channels are sized to meet the individual material specs. The layer thickness of the individual material melts are corrected and optimized by means of built-in-adjustment sleeves.
There are many other variations of wall designs. The ACCU-HEADS are available in sizes Type A 25 (25 Liters ≈ 6,6 gal.) up to Type A 400 (400 litres ≈ 106 gal.).
As an inherent feature of the discontinuous COEX technology, the extruded melt is stored in the accumulator head while constant pressure and temperature have an optimum effect on the bonding strength of the single plastic layers. Contrary to continuous co-extrusion techniques. RIKUTEC’s COEX technology helps to keep the parison from stretching lengthwise by relatively short ejection time and by virtue of a constant melt temperature maintained in the process of forming and blow-molding of multilayer articles with length up to 7 m.
REDUCED MATERIAL COSTS
The RIKUTEC COEX technology offers savings in material costs because the container wall can be custom designed to meet specific product requirements. For instance, the outermost and innermost layers can be composed of virgin high molecular PEs, while cost effective recycled materials can be used for the intermediate layers.
Thus the RIKUTEC COEX technology is also environmentally friendly.
APPLICATION EXAMPLES
- ACCU-HEAD TYPE A COEX 2
for 2 layer coextruded wall designs e. g. internal layer – virgin material, external layer – pigmented colored material. - ACCU-HEAD TYPE A COEX 3/4
for 3/4 layer coextruded wall designs e. g. use of recycled materials contained in virgin material. - ACCU-HEAD TYPE A COEX 5
for 5 layer coextruded wall designs e. g. containers with barrier layers.
There are many other variations of wall designs.
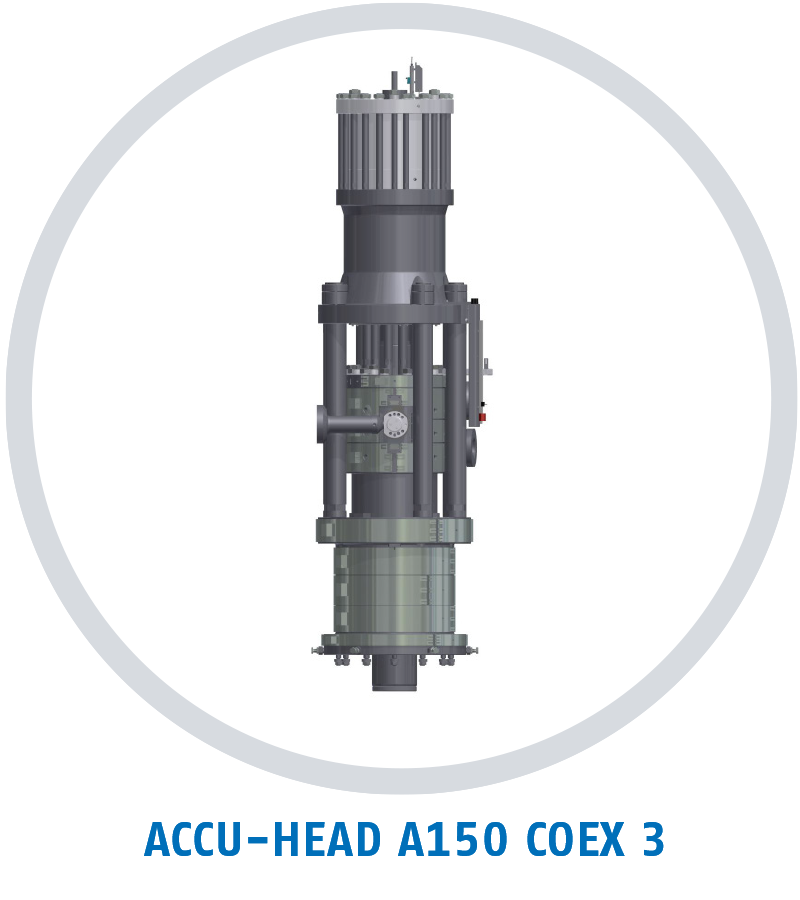